Special Projects
The Project of a Lifetime
Jim and Mike have lived in their beautiful, historic home on S Street NW, near Dupont Circle, for many years. This corner residence is as large as an apartment building and as an older structure (circa 1880’s) with many special internal and external design features it takes a caring hand to maintain and preserve its original beauty.
Jim and Mike had been challenged for years about how to deal with their leaking roofs and had seen an article in a local newspaper about our work on historic roofing projects in Capitol Hill and Georgetown. A meeting was arranged and a walk through of the upper floor (to see the internal damage) and the roof exterior revealed that Jim and Mike had “The Project of a Lifetime!” They were committed to having us do what was necessary to restore the roof and related structures to their original state using natural and historic materials.
We're talking about replacing:
- copper roofs
- copper gutters and downspouts
- huge copper water table (aka built-in-gutter or "Yankee" gutter) that extended around most of the circumference of the house
- large slate dormer roof
- tall and very steep slate turret roof
- multiple skylights
- main flat roof
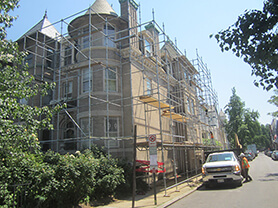
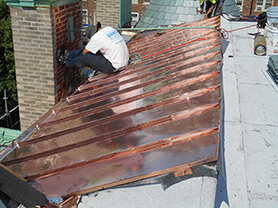
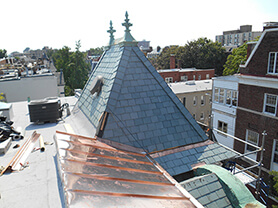
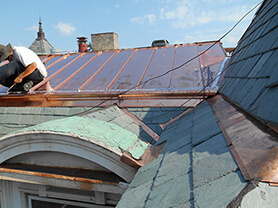
This type of work keeps roofers up at night! The work requires many areas of expertise and also project management skills to ensure the work is done professionally and in a timely manner.
As a first step (after obtaining multiple DC government permits) a large scaffolding structure was installed from the ground to the rooftop, at a height of over 50 feet and all the way around the house to allow our project teams to do their work. For this part of the project alone, it would take nearly a week to set up the scaffolding. Special materials and unique expertise would be required for this job. Three teams of roofing experts, each with different areas of expertise, would be needed. Thousands of pounds of old roofing materials would need to be removed, piece by piece, and hauled away for disposal to designated disposal sites.
The many skills required for this project included sheet metal specialists, high level carpentry expertise, slate tile removal and installation expertise and scaffolding experts. Each workday, the crews were required to make their way up the tall, narrow scaffolding ladder and wear their safety equipment.
A natural stone slate roof is one of the most durable roofing systems you can install on a home. For this project we also needed to source a specialized green colored tile. If properly installed, using the right materials, the roof will last for well over 100 years and is an investment that will increase the value of your home. The crew chief and team of installers must have the ability to cut the stone, fit it to the underlying wood and attach it using copper nails, all while working in difficult and potentially dangerous conditions. This is no task for a novice!
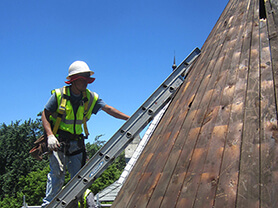
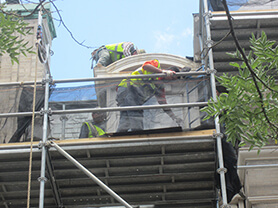
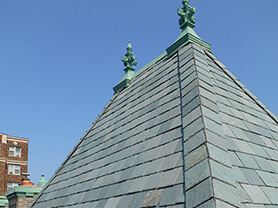
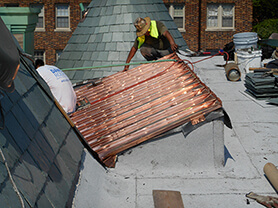
After measurements by our sheet metal crew, hundreds of square feet of standing-seam copper had to be tailor-made and fabricated at a specialty sheet-metal shop. These panels had to be transported to the job site in extra large trucks and were installed section-by-section. For the copper water- table, rolls of copper were delivered and the crew carefully measured the surface, cut the copper to specifications and hand crafted the copper into the finished product. While other types of metal were available as an alternative, the owners chose copper for its long-lasting ability to withstand many years of wear and tear and the aesthetic appeal of this original and historically accurate metal.
The low-slope main roof and skylights were installed by our third crew to complete the work.
The project was now complete; a timeline that lasted nearly 3 months from set up of the scaffolding to its removal after all the roof work was done. This "Project of a Lifetime" was a most exciting and challenging project for us and one which Jim and Mike will enjoy for many years to come.
There Are Castles in Capitol Hill
Well, not exactly castles but castle-like appendages; slate turret roofs all over the Hill! Walk on the 1200 block of E St. N.E. or the 200 block of 8th St. S.E. and there are more than 40 houses on these two blocks alone that have slate turret roofs. When you add these to the hundreds of additional houses in Capitol Hill that have slate turret roofs or slate mansard roofs we’re talking a lot of slate!
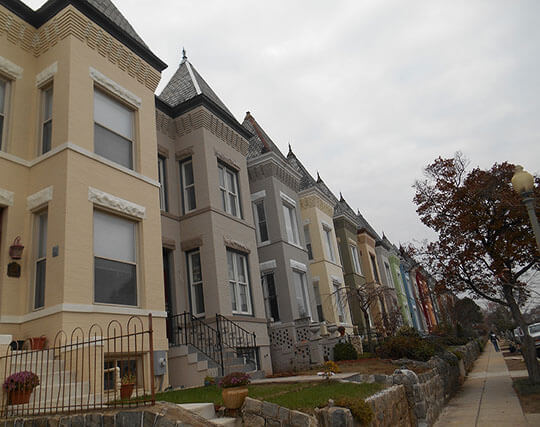
Slate is a fine-grained, foliated, homogenous metamorphic rock derived from an original shale-type sedimentary rock compound of clay or volcanic ash. Sounds technical doesn’t it! For our purposes slate is a natural, stone-like tile; a historical roofing product that can last 100 years or more and comes in a variety of colors. Slate tiles are frequently gray but also are available in green, red, cyan (greenish blue) and some other colors.
A turret roof is a pointed, almost projectile looking structure that was very common on old castles and can be found all over D.C. in Capitol Hill, Georgetown, Dupont Circle and many other sectors of the city. These roofs are beautiful, historic and add much charm to this city. There are very few cities where you can find these types of row houses.
For this special project, we have customers, Mike and Andrea who live on the 1200 block of E St. N.E. Most of the turret roofs in this block are still original, well over 100 years old. These old roofs, while beautiful, do eventually create serious problems for homeowners. They are many different ways for water to get into the house. Tiles disintegrate and expose wood to the elements or the connection to the underlying wood decays and tiles slide down below or onto the ground. Nails fall off, connecting seams erode and old repair work wears out. Below most of the roofs is a metal built-in-gutter (BIG) that collects the water that drains off the slate tiles. Over time the metal also deteriorates and has to be repaired and eventually replaced. We see a lot of these structures that have badly decayed wood underneath because of all the years of water seeping in.
For roofers, these are very difficult and dangerous projects to take-on. It’s not as simple as putting up a ladder and working on a flat roof. Special equipment is needed, including possibly scaffolding and very high level roofing expertise is required.
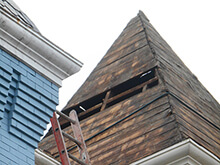
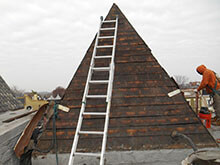
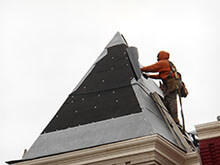
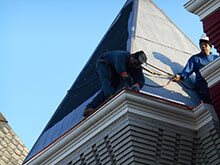
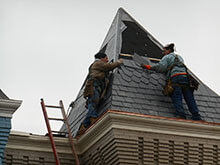
Mike and Andrea had an original turret where tiles were missing, water was leaking into the house and many repairs had been done over the years. We were called in to do an inspection and make recommendations after they had read about our company in Mom’s On The Hill listserve. It was clear after just a few minutes that the roof and BIG could not be salvaged and that a new roof was needed. Like any roofing concern there is a point in time where repairs just won’t do the trick and a new roof is the only viable option. This was one of those times.
Without providing too much technical, boring detail, one of the best aspects about this type of project for a roofing company is that it is true, artistic, historical roofing at its finest. The slate tiles and the copper have to be hand cut to specification, properly aligned and patiently applied. You could call this “bespoke” roofing. Like bespoke tailoring the roofing materials are tailor-made and customized to fit the structure and every project is different.
We hope you enjoy the photos of our work!
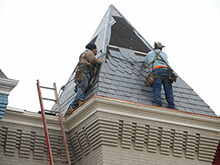
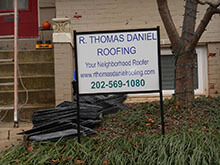
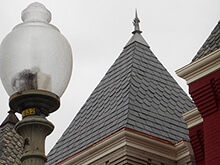
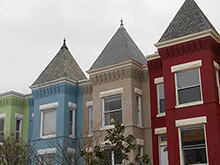
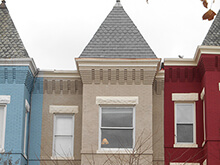
Capitol Hill Commercial Roofing Project
Capitol Hill is considered to be one of the most family-oriented, walkable and close knit communities in the entire DC area. The beautiful, mostly brick, row houses have many different architectural styles including Queen Anne, Federal style, Richardsonian Romanesque and numerous other styles of architecture. The different choices of the original builders easily add to the charm of the Hill.
It is easy to overlook the many multi-family residential buildings on the Hill that are usually mixed-in with the row houses. These condo buildings, apartments, converted churches and schools offer many different lifestyle choices to the both families and the single community that is also thriving on the Hill. Many residents are Hill staffers for Congress and the Senate, associates at downtown law firms, employees of associations and non-profits and the occasional member of Congress and the Senate.
These buildings are usually owned by family businesses, real estate partnerships, apartment investors and the like. The roofing problems of the building owners are not dissimilar to the problems of individual homeowners. The buildings usually have flat and low slope roofs that need routine maintenance and replacement after a long period of time. But there are numerous other challenges to the owners and roofing firms doing the work on these buildings. Often there are numerous HVAC structures, satellite dish platforms, large vents and multiple skylights on these buildings creating a complex situation for the replacement of the roof.
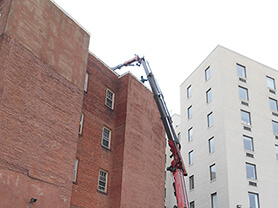
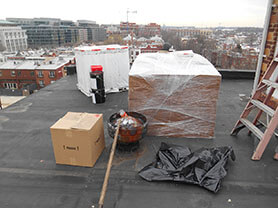
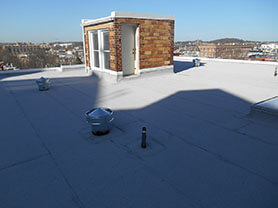
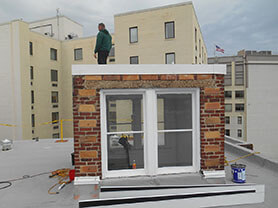
Our firm has replaced numerous roofs on these larger buildings on the Hill and one such project was near Union Station at Third Street and Massachusetts Ave. NE.
The building is a large 30+ unit apartment building that was built many years ago and is attached to two different office buildings. But, directly across Third St. is a residential neighborhood of typical Capitol Hill row houses. The building height is 80 + feet and abuts the sidewalk on Third Street and a parking lot on the side. It is a 5 story building with no elevators. The roof was an older rubber roof that was at the end of its useful life and needed to be removed and replaced with a new modified bitumen roofing system. The tactics to do the job were challenging and complex. The roof was too high to access by ladders. It was also determined that scaffolding to get access to the roof was not feasible because we could not block the busy sidewalk for a week or more and the parking lot was used by the commercial tenants of the adjacent building so we couldn’t utilize that space for scaffolding.
The only possible solution to load the roofing materials up to the roof was to utilize a large boom lift encased in a mobile truck housing unit parked in the parking lot and to do the loading on a Sunday (when the lot was not being used). The old roofing materials would also have to be off-loaded using the boom lift from the roof down to the ground. The entire project took about a week and the roofing crew would access the roof by climbing the 5 flights of stairs each day. It’s a lot of extra work when you consider the physical nature of roofing work in general!
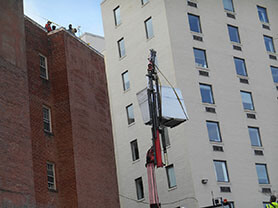
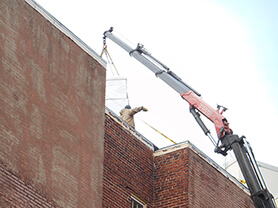
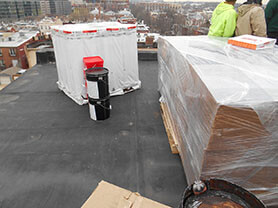
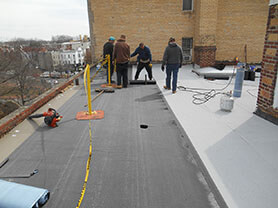
Our firm has replaced numerous roofs on these larger buildings on the Hill and one such project was near Union Station at Third Street and Massachusetts Ave. NE.
The building is a large 30+ unit apartment building that was built many years ago and is attached to two different office buildings. But, directly across Third St. is a residential neighborhood of typical Capitol Hill row houses. The building height is 80 + feet and abuts the sidewalk on Third Street and a parking lot on the side. It is a 5 story building with no elevators. The roof was an older rubber roof that was at the end of its useful life and needed to be removed and replaced with a new modified bitumen roofing system. The tactics to do the job were challenging and complex. The roof was too high to access by ladders. It was also determined that scaffolding to get access to the roof was not feasible because we could not block the busy sidewalk for a week or more and the parking lot was used by the commercial tenants of the adjacent building so we couldn’t utilize that space for scaffolding.
The only possible solution to load the roofing materials up to the roof was to utilize a large boom lift encased in a mobile truck housing unit parked in the parking lot and to do the loading on a Sunday (when the lot was not being used). The old roofing materials would also have to be off-loaded using the boom lift from the roof down to the ground. The entire project took about a week and the roofing crew would access the roof by climbing the 5 flights of stairs each day. It’s a lot of extra work when you consider the physical nature of roofing work in general!
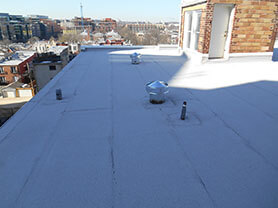
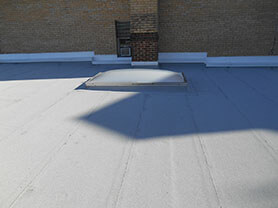
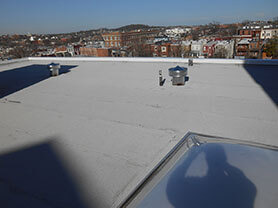
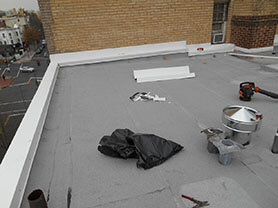